By Charlotte Wiederholt, President, Studio Other
Studio Other is made up of a diverse group of creatives, makers and builders who value the art of craftmanship both within and beyond their job description. In the time spent outside of the office, you’ll find many of our people working on their artistic endeavors, crafting primarily with their hands and using various mediums. In what feels like a lifetime ago, our team was working on Studio Other projects in a similar manner, drawing up sketches on pen and paper and presenting every idea and revision in person. While there’s certainly a level of nostalgic appeal in using analog methods, the bottom line is that they allowed for slow turnaround, inefficient manufacturing and room for error.
Over the years, we’ve added technological programs and advances to our collection and in turn, we’ve watched our business grow and improve substantially. In fact, we utilize technology at every step of the co:design process, as it improves our communication, efficiency and, ultimately, innovation.
Design
SketchUp is imperative to the initial co:design process because it allows our design engineers, partners and clients to create and modify designs live and simultaneously. This means that we can iterate 3D sketches live with our clients, allowing the real-time conversation to lead the creative process. Before SketchUp, we would draw out sketches using pen and paper, schedule an in-person meeting, receive feedback, make modifications, send it back and repeat. Now that we’ve done away with the clunky back-and-forth of hand-drawn sketches, we’ve reduced the time spent at this step from one week to two hours. And possibly most importantly, the increase in client engagement and hands-on, direct feedback throughout the creative process has led to invaluable relationships that last well beyond the initial project.
Engineering
Prior to technological advances, we relied on attention-to-detail, guesswork and rounds of revisions to prepare product for manufacturing. Today, SolidWorks, a 3D engineering software, allows our engineers to take our SketchUp model, convert them to SolidWorks parts and prepare it for production by analyzing structure, tolerance and exact sheet yields. Because all 3D solids are parametrically linked to drawings and automatically update, the verification process is seamless and 100% accurate.
Years ago, we would draw every part in 3D in AutoCAD. Today, all parts are fabricated from a .DXF or .DWG file that originates from the complete SolidWorks assembly. The program allows us to build each separate part both individually and all together. This is extremely valuable because if we need to update one part, the program will build and reload it into the assembly to allow us to preview how the pieces will fit together and see if they align.
Sourcing
Because every part is manufactured from a SolidWorks file, we have the opportunity to use several different manufacturers to get the same part. This is an important capability from the client’s standpoint because we can massively cut down the turnaround time by spreading the quantity of pieces needed over several manufacturers to scale up and complete the process quicker.
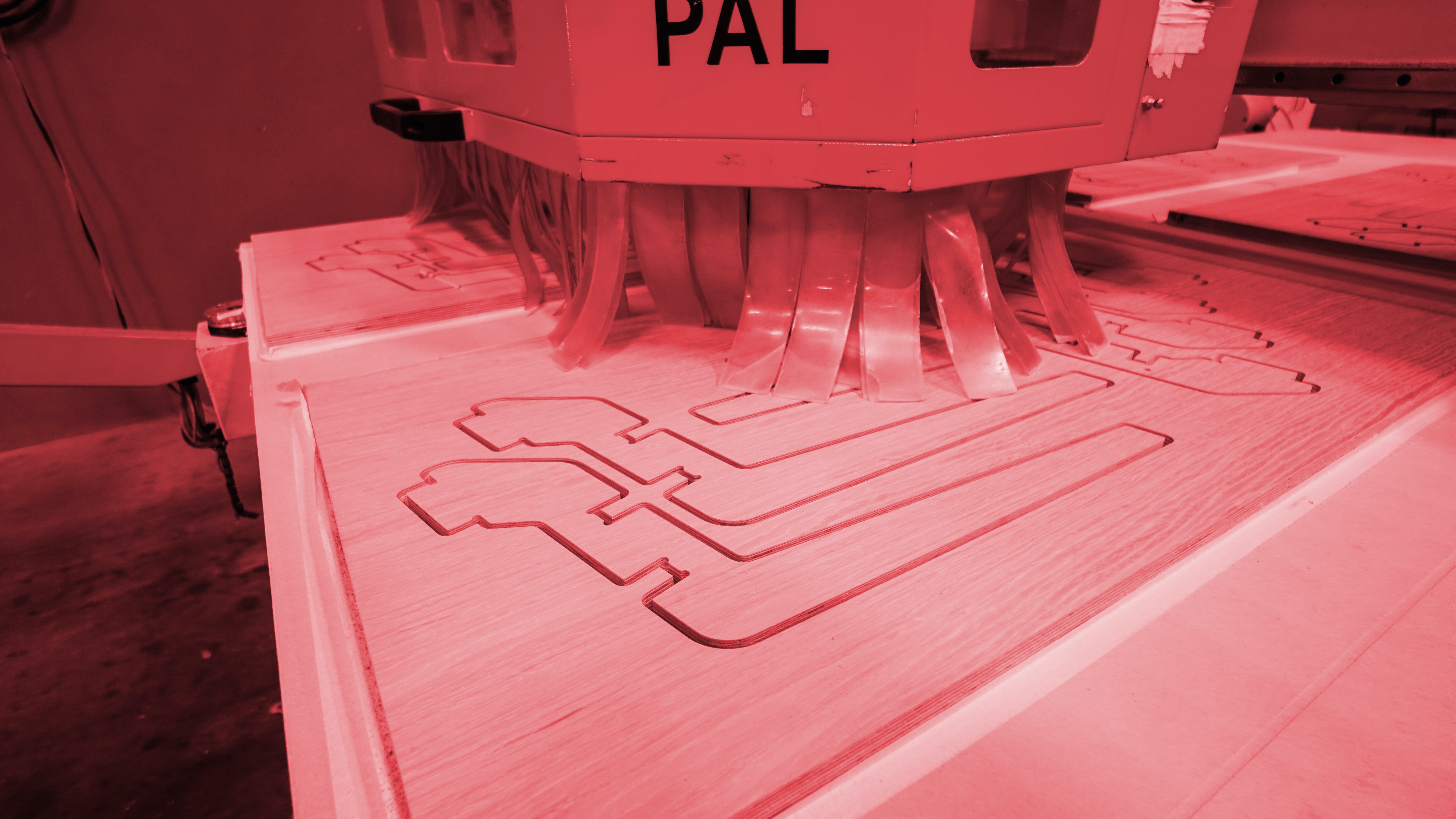
Manufacturing
Advanced manufacturing tools have allowed for mass production, making it possible to create eight replicated parts just as easily as 80,000 replicated parts. Thanks to laser cutting, configuration machines, 5-axis CNC router technology and 3D printers, accuracy is near 100%, ensuring that all products will be manufactured and replicated without error.
Future Product Add-Ons
Before technology brought us to where we are today, if our client returned to us requesting to add or replace product, we would have to start at ground zero and expect a substantial turnaround time. Now, if our client were to return years later requesting more of the same workstations or conference tables due to company expansion, programs such as SolidWorks and a CNC router allow us to easily duplicate the exact same parts of each product. This also enables us to replace and modify each individual piece of the product—either piece by piece or in bulk—giving us the opportunity to grow and evolve with our clients.
Complexity
The use of technology has allowed us to model and build very complex, detailed and unique designs. Years ago, we were limited in the creative liberties we could take with our designs and confined to easily manufacturable qualities, such as 90-degree corners and basic shapes that did not place much focus on connection points. This was because every detail that strayed too far from the typical shape would need to be hand-implemented. For example, we worked on a project 12 years ago with an architect who wanted rolled steel panels for every desk. We took our drawings to the metal suppliers, who then needed to take each four-foot panel, drop the break press about 100 times on it to slightly bend it to the correct radius, then hand-sand the break marks out. Ultimately, a design as unique as this one was labor intensive, expensive and difficult to guarantee perfect iterations.
Technology is at times regarded as a necessary evil that removes the human element or “soul” from the art of creation. While this may be true in some cases, we at Studio Other feel that it has opened the doors to boundless creativity and innovation free from the constraints of manufacturing limitations. In fact, we have had the opportunity to produce similar customized rolled steel panels for several clients, such as Foley Hoag and Boston Consulting Group, in the past few years with absolute ease and within budget—a night-and-day comparison to our endeavor 12 years ago.
Ultimately, Studio Other is made up of makers and doers at heart. We find fulfillment and value in our job through the relationships, collaboration and innovation we experience with every project—and digital advances have allowed us to participate to our highest potential in each of these areas. At the end of the day, we’re a bunch of creatives who like making our clients’ wildest dreams a reality in any way we can. When you’re ready to start your own co:design process, we’ll be there to meet you and say, let’s make cool sh*t.