Betty is a Sr. Industrial Engineer within the Studio Other Team. His passion to create is what initially led him to Studio Other, and what continues to drive his hobbies outside of the office. Currently, you’ll find him busy making hand-strung art and custom cutting boards using recycled leftover materials from Studio Other projects. Beyond art-related interests, Betty loves camping, anything involving nature and costume contests.
What’s your name?
Jason Betty
Passion project name?
Custom Cutting Boards
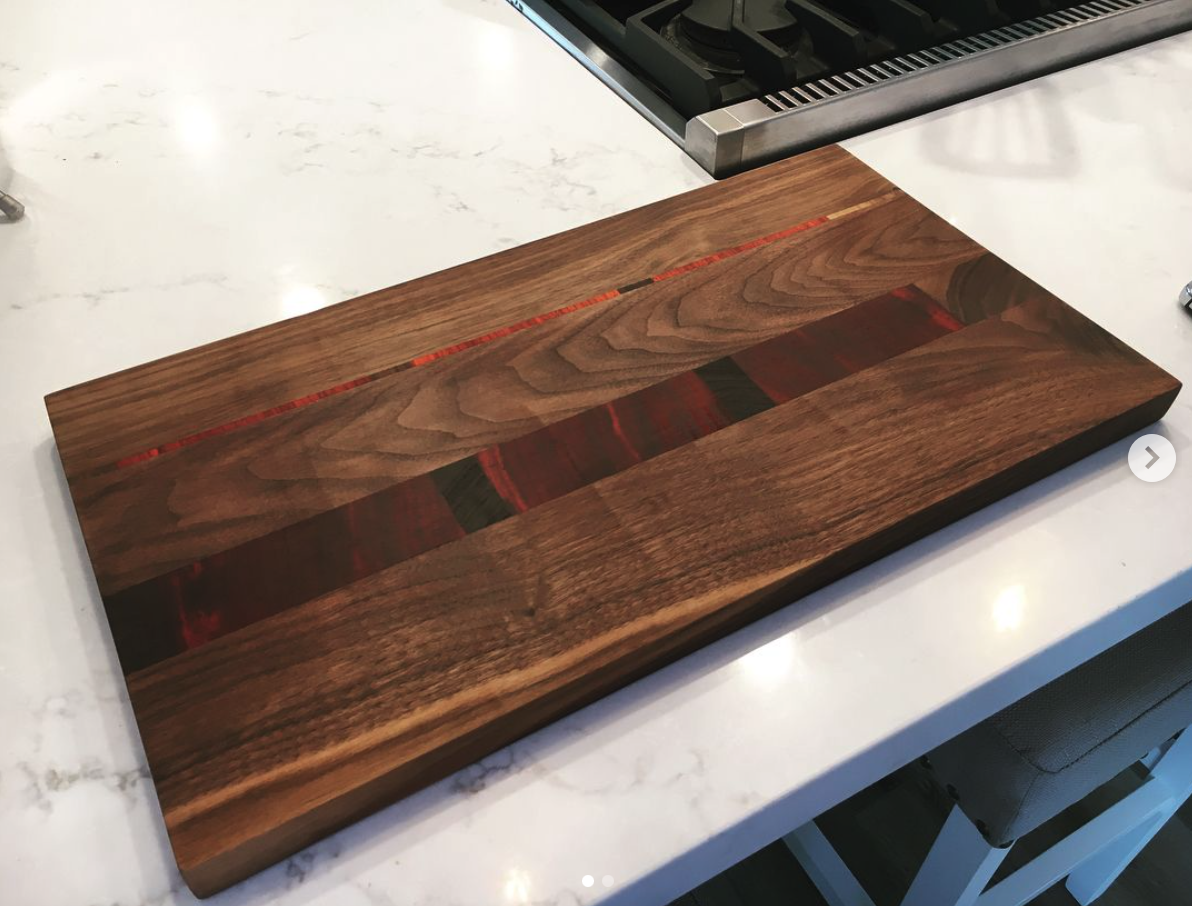
How would you describe your designs?
While the designs of my cutting boards are traditional in shape, my priority is to enhance the wood’s natural features and intricacies with careful treatments. Additionally, I like to play with colorful elements and unique edging designs to give personality without compromising functionality.
What or who was your inspiration for this project?
The wood itself. Simply put, I cut and piece the wood together in various ways until a specific design speaks to me.
How long does it take to build a cutting board?
About four working hours per board depending on the design complexity.
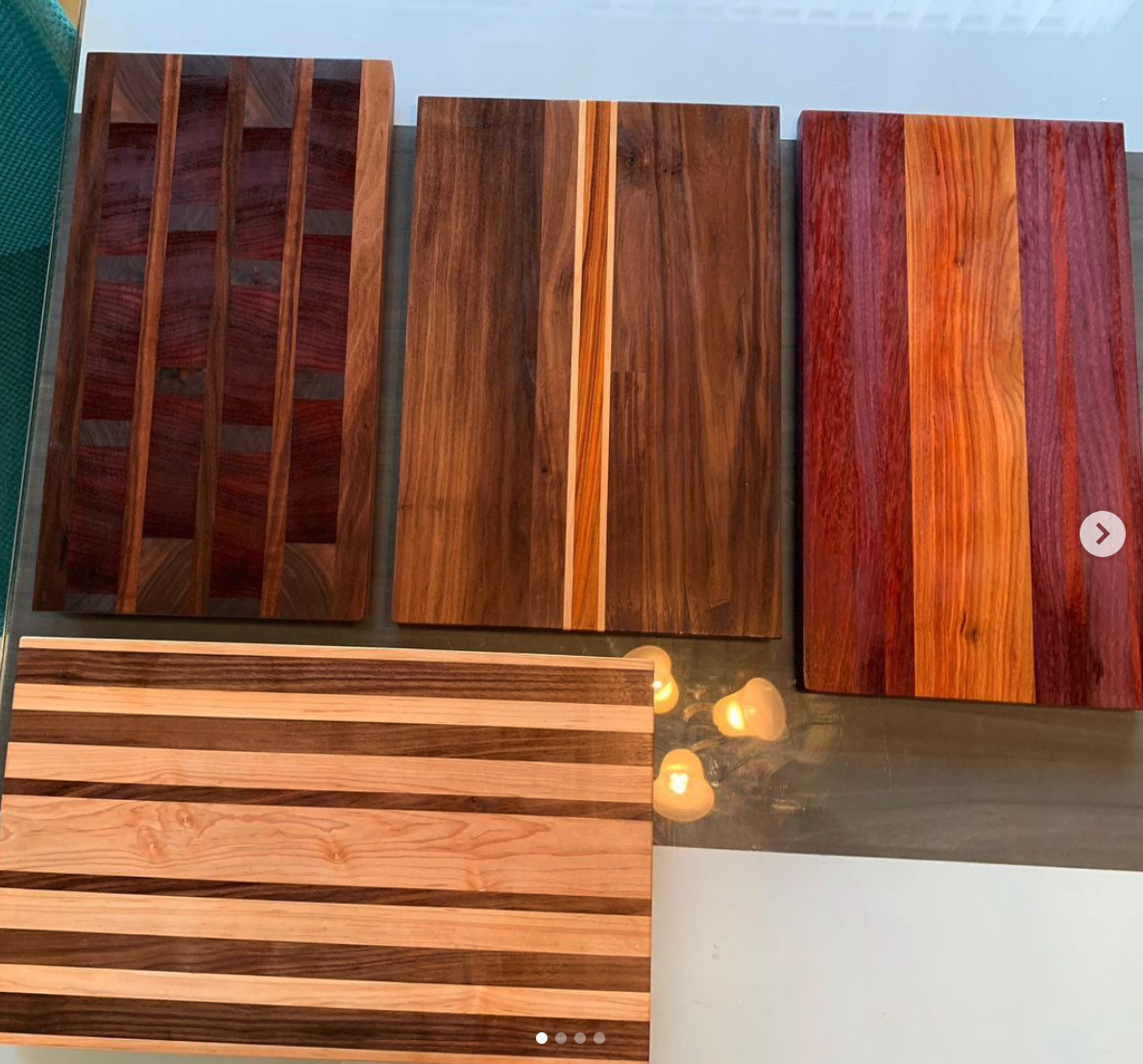
What materials are used?
I use a wide variety of both exotic and domestical natural woods — from hard maple and walnut, to canary wood and African padauk — to give the pieces a splash of color.
What’s your building process?
I first cut the raw lumber into the desired sizes for the design, then I glue and clamp the parts together. Once dry, I sand and plane the boards until they’re perfectly smooth and flat, adding edge details as desired. Then I raise the grain with a wet cloth and re-sand the board. Using a cotton cloth, I apply mineral oil to both sides, let it rest for 20 min, and reapply two more times to “season” the board. Mineral oil provides a natural moisture to the grain that prevents it from drying out and cracking. Additionally, it helps to increase wood’s natural antibacterial qualities and its resistance to water. Finally, I wipe any access oil off and the cutting board is complete.
What was the greatest obstacle in the process and how did you overcome it?
Designs that require multiple glue ups, where you connect different types of wood, are the most difficult because it can be tricky to line all the seams up correctly. I’ve found that the best ways to avoid mistakes are to make sure your parts are cleanly cut and to pay very close attention during the gluing process. A steady hand and attention to detail can go a long way.
Any additional or unique information about the project we should know?
I recently made an extendable and foldable version that is meant to act as a cutting board in the kitchen of a converted van. I was able to successfully build this design by using shelf drawer slides and adding hinges on the bottom side of the cutting board.
Shop Jason's custom cutting boards at SoBayHandmade