Stephanie is the Operations Manager within the Studio Other team. Her favorite aspects of her job are collaborating with amazing people and seeing initial design inspiration turned into reality. On the weekends, you’ll find Stephanie spending time with her family and occasionally adding to her tattoo collection.
What’s the best part about working for Studio Other?
I love the people I work with. They have become more of a family and not just coworkers — I even had two tables reserved for them at my wedding.
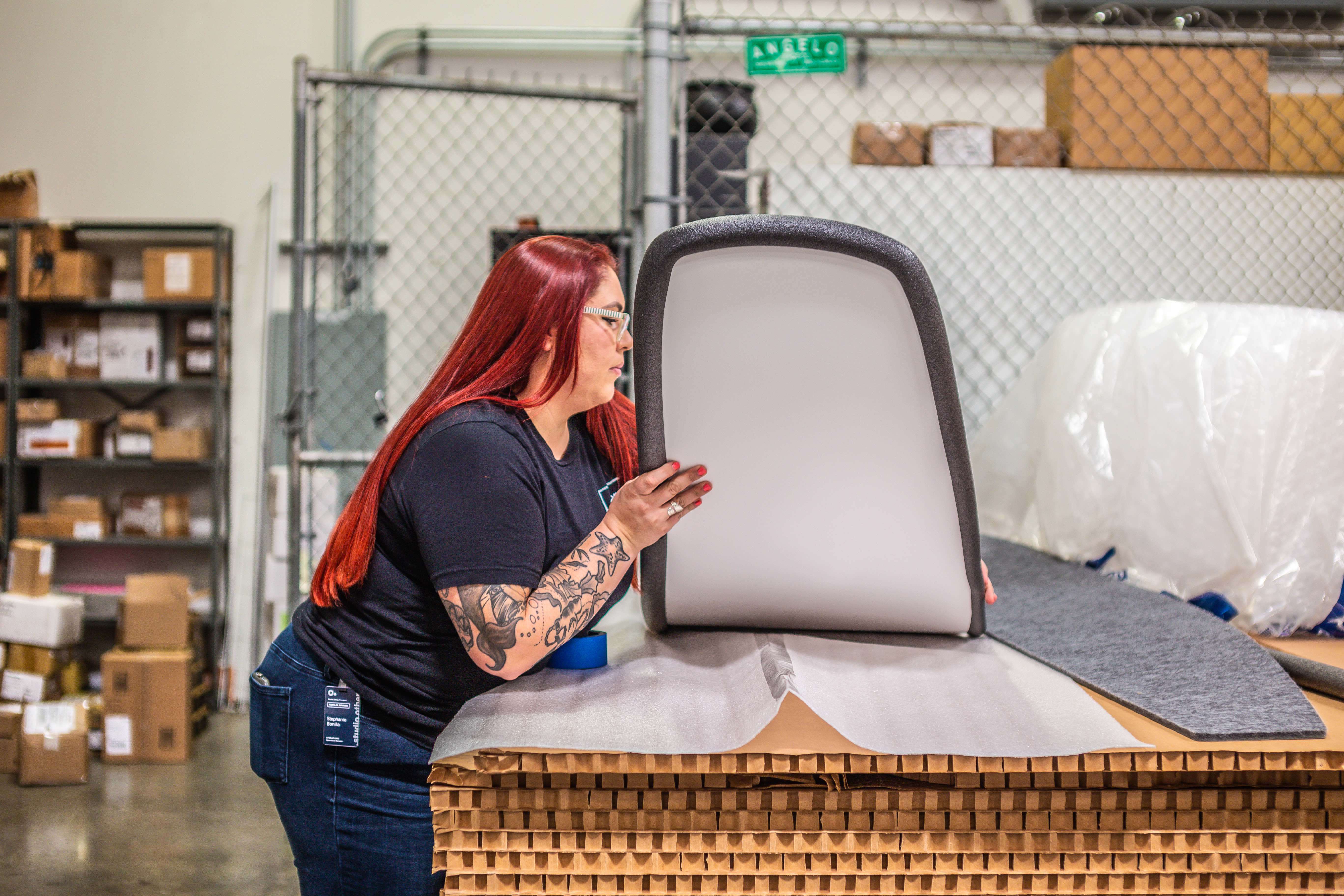
What do you most enjoy about your specific role?
I love ensuring everything goes smoothly at the installs. I enjoy making clients happy and seeing them walk the space once their installation is complete. When I have a project that goes smoothly and has zero punch items, it is the best feeling in the world.
Why is quality control important to the overall process?
QC is probably one of the most important parts of our process because delivering a perfect product begins with QC. We have a very strict QC standard for all of our product, so we take the time to inspect every item and make sure they are all in perfect condition. If product does not meet our standards, then we do not ship it. We also take our pack out very seriously — I pride myself in knowing that we ship product properly packed that allows for little to no freight claims.
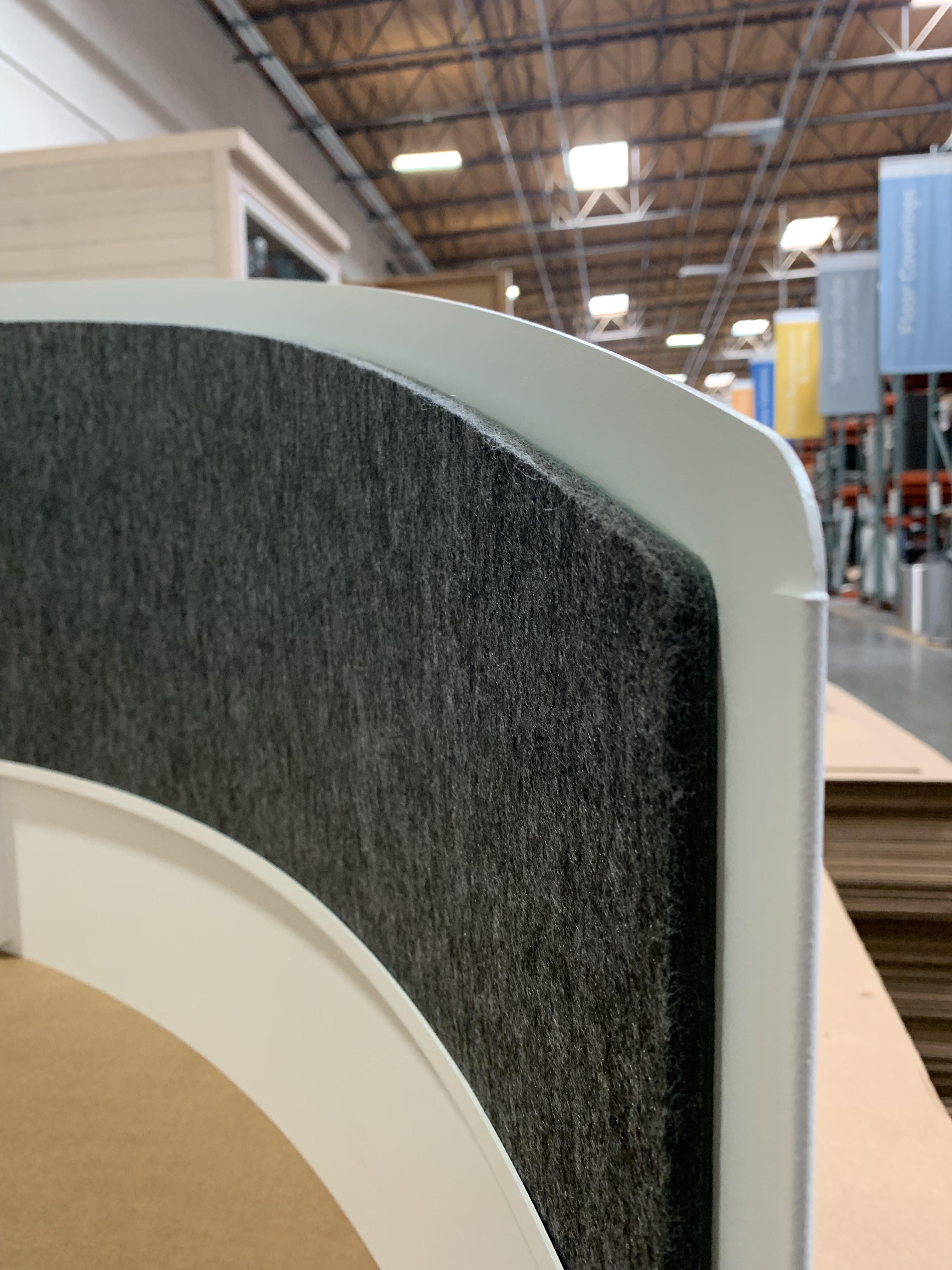
Can you walk us through the quality control process at Studio Other?
We begin the process by carefully inspecting each panel so that it passes our quality control check. We look for the following:
Finish quality of powder coat
Welds
Felt quality
Overall fit and finish
We then assemble the felt panels into the shell and individually wrap all of the panels. Lastly, we place all of the panels on pallets, secure, and build the crate. The products are now ready to ship to our clients for install.
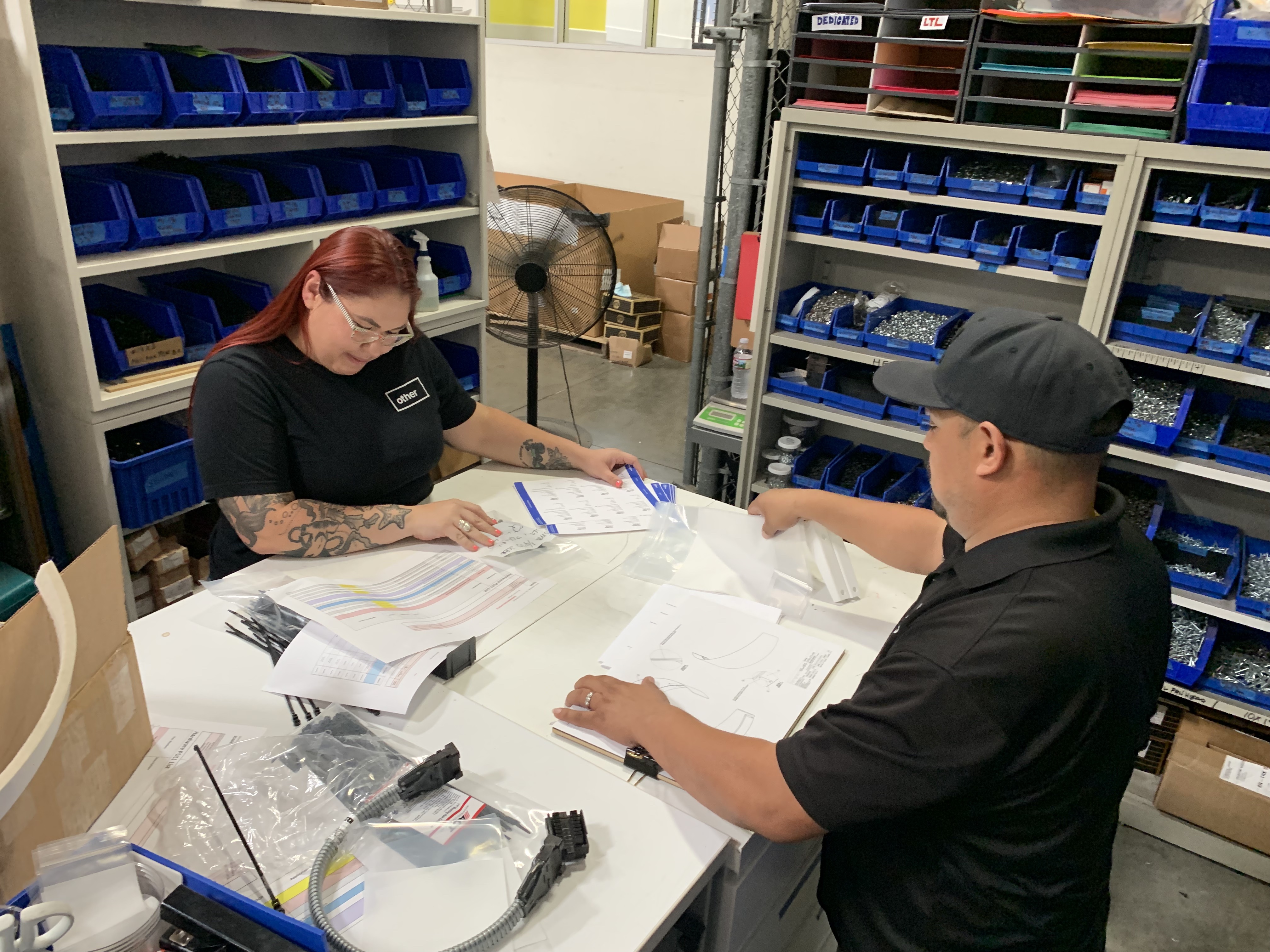
What has been the biggest quality control challenge and how did you overcome it?
Our biggest challenge has been standardizing the QC product checklist. My team has spent a lot of time coming up with a rigorous checklist that each piece must pass in order to ship out to our clients. We are constantly striving to improve our product and are only improving with every project.
What is your favorite project you’ve worked on and why?
My favorite project to work on was Live Nation. I worked closely on that project from the very beginning to the hand-off to the client at the very end, and I was on the job site at least once a week or more making sure that everything was going flawlessly. Seeing a project go from sending POs to vendors, to QCing product at our warehouse, to loading on our trucks and offloading onsite and to being fully installed was an amazing process. This project included over 100 private offices and almost 500 workstations, and yet our punch was very minimal. To know that we finished a project without any major issues was a huge accomplishment.